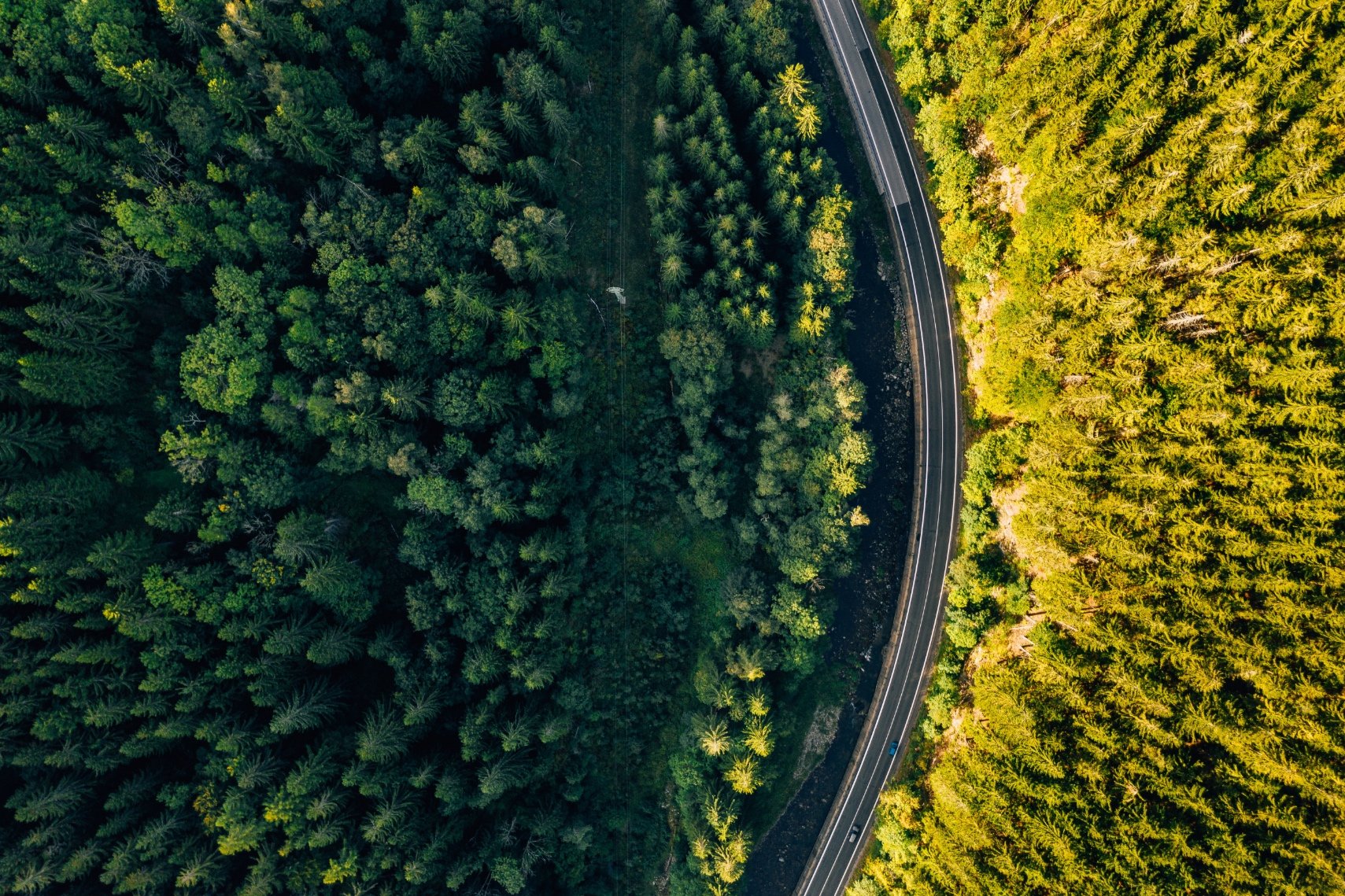
Bringing three vital ecosystems of waste, hydrogen, and transport together in one solution.
Hydrogen-capable Plasma Assisted Gasification
Chemistry and physics…
Gasification not combustion.
Energy applied to H20 water changes its state from solid ice to liquid water, and then from water to gaseous steam. With more energy applied, gases become ionized and turn into a superheated plasma state, the fourth state of matter.
A plasma torch produces a direct stream of plasma that reaches temperatures between 3,500º and 4,000º C. When that stream is directed at solid materials like biomass, plastic and metals, molecular chemistry transforms that solid into its molecular components. The plasma process produces a high-quality syngas without any of the toxic by-products.
HPAG an enabler for zero emissions mobility and transport
HPAG is an advanced clean and highly efficient molecular recycling technology, utilising renewable energy, enabling recovery process of resources to provide low-cost green hydrogen environmentally and economically efficiently. The advanced technology, refined and proven over 40 years of development, utilises the higher order technologies of:
pyrolysis, the thermal degradation of organic materials in the absence of oxygen at between 250°C to 700°C;
gasification, those thermal-chemical processes at between 500°C and 1,600°C used to recover the chemical value of resources; and
plasma, a physics process where ionized substances become highly electrically conductive. Utilising extremely high temperatures (over 3,500°C) to break-down hazardous contaminants such as PCBs, dioxins, furans, and pesticides, into their atomic constituents. Highly efficient, the gases created are cleaned, with a vitrified inert residual slag created.
Scaleable, modular
Importantly, overcoming the shortcoming of incineration, the HPAG process has been developed to be scalable, modular, process efficient and cost effective enabling environmentally safer localised developments (with lower transport costs and energy leakages).
HPAG's small plant footprint (less than 3,000 m2), scalability for applications as low as 8,750 tpa, low environmental impacts and limited inter-dependencies provides maximum optionality for smaller regions and for locations nearby to resource recycling centres, landfills, power transmission and distribution infrastructure, existing pipelines, and transport routes.
Aligned with recycling and FOGO
The modular design approach that scales to the input supply also mitigates the need for contractual guarantees of large waste volumes.
This avoids the needs for all encompassing lock-in waste feedstock contracts (and associated gap penalties) that operate counterintuitively to aspirations to increase recycling targets and embracing emerging FOGO composting ambitions.
All aimed to divert landfill waste and reduce carbon emissions.
Minimal emissions
The integrated HPAG pyrolysis, gasification and vitrification processes utilise plasma torches and generate extremely high temperatures, radically lowering the levels of emissions - up to 90% less in absolute terms and demonstrated to be far below EU BREF standards that many combustion incineration plants struggle to meet.
HPAG processes splits out from the syngas and is captured for downstream uses, including creating green methanol. This provides major advantages over incineration that emits large amounts of post-combustion CO2 with its flue gas.
Combustion incineration being the burning of resources with oxygen at between 800°C and 1,450°C creates significant toxins requiring post combustion treatment, and ash. In the EU, the combustion process is used in 99.5% of all incinerators, used to source low grade energy and district heating.
No ash, with captured CO2 emissions
HPAG processes produce no ash, in contrast to the 15% to 25% Incineration Bottom Ash and 2% to 5% hazardous 'fly ash' (Air Pollution Control residue - APCr) produced by combustion incineration (weight being a percentage of initial waste treated).
Increasing regulatory pressure on environmental performance (bottom ash and fly ash containing Per-and polyfluoroalkyl substances (“PFAS”) and Persistent Organic Pollutants (“POPs”), flue gas emissions of NOx, particulate matter, and other pollutants), high water footprint, low carbon emission outcomes and large capital expenditure requirements are seeing combustion incineration being replaced by newer technology.